Elements of Intersection between Quality Management and Requisite Organization
- The macroeconomic impact of how quality builds itself and eventually takes the market from the opponent. We have not yet developed the seven tools in terms of quality. The biggest bang for the buck is that there are seven tools.
Speaker A I was Dr. Deming's assistant at Columbia for two years before he died. So I was somewhat familiar with his approach and how you structure things. And basically he went to Japan in 1950 in or...
Transcript of the presentation video
NOTE: This transcript of the video was created by AI to enable Google's crawlers to search the video content. It may be expected to be only 96% accurate.
Speaker A I was Dr. Deming's assistant at Columbia for two years before he died. So I was somewhat familiar with his approach and how you structure things. And basically he went to Japan in 1950 in order to teach quality to Japanese and their invitation. And so he went there and he put on the board several things, but one of which was this, which is production as a system. It's a cycle to jump a little bit. Six Sigma is one of the children of Deming's quality approach. So don't think that it's a child and we'll get into that, but it's very related to quality and so forth. It's related to it basically production as a system. In this case, Deming is talking about open systems. It's open at both ends, the supplier and the customer. Now you'll notice that you have the supplies of materials coming in and put it up a little bit higher. You basically test of the process of the machines, of the methods, and you have receipt and test of the materials. So you're using statistics to measure what you're looking at to find out whether it fits your system or not. Now you have various stages to which the raw material coming in from the suppliers, the parts coming in from the suppliers goes through production, assembly, inspection and distribution and finally out to the customers through your distribution system. Now you'll notice that it's open ended in terms of the customers. What happens then is you have your customer research here. The customer research can take place immediately or six months later or a year later, doesn't matter. You're looking to find out how the customer is using your material, your product or your services and whether the customer is satisfied. And so that then comes in at design and redesign and what is the nature of organization? What organization? What you have here, design and redesign of the system, including the annual differences that take place, the sizing of production and assembly, inspection and so forth, and a distribution. So how do you size your units? Depends on the nature of what you're producing. So you have here essentially at production, assembly, inspection, distribution, you have a unit that does it, plus a first level supervisor. So basically you're talking about the first two levels here in this horizontal linkage headed up by stratum three manager, who's part of the function of stratum three manager is to design the units under him or her. What you're looking at here in terms of Jackson damning, is that Deming is looking at the operations of a firm straight across, basically where the rubber meets the road. The bottom. What Jackson Brown are looking at is the vertical system and the vertical system, the two overlap somewhat. They overlap 20%. By rough estimation, it means 80% of what Deming wrote about had nothing to do with Jacks, had nothing to do with the upper portion at all. And conversely, 80% of what Jackson Brown wrote have nothing to do with Deming. They're just standalone, not neither good nor bad. With the two overlap together, you literally have about 15% where if you know Jax and Brown on one hand and you know Deming on the other hand, you can make a choice as to which one applies better and you go with it. That leaves a hard knob of about 5% where you literally flip a coin. My choice, you end up with one third Deming, one third Jackson Brown, and one third you're going to have to figure out what's going on. You're on your own. Reality may be outside of any answer that you'd like to give. Now, one of the things that Deming put on the board also at that meeting in 1950, this is taken from his book, is something that we don't have, that we ought to have eventually we don't have, which is the macroeconomic impact of how quality builds itself and eventually takes the market from the opponent. Okay. Now you have to understand at the very beginning, before your time, at the very beginning, quality costs money. In the very first book on quality, because Quality Is Free by Philip Cosby and he's trying desperately to counteract that image. Well, when you're dealing with guilds and you're dealing with the quality of a person and their ability in the hand, it costs more to hire someone who's very proficient at what they do, who has the skill. So as a result, the hiring of skilled workers costs more. So therefore you go with mass production. Taylorism which going to a small time. But the real question is, in terms of the macroeconomic issue, how does this actually create value? In this case, you just start by improving your quality, which costs you nothing very little. Your costs decrease because of less rework and fewer mistakes, fewer delays, fewer snags, better use of machine time and materials. You improve your quality, productivity improves as a causal outcome of that. Then comes capturing the market with better quality and lower price because you have a lower price because you have better flow through, more stable flow through. You stay in business, then you provide jobs and more jobs and then you start the cycle again. So this is how you create jobs. And in Japan, particularly after Second World War, you only had human resources as your resource. You had no physical resource, only people. And that's what they built their entire thing on, people. Now, most of us are familiar with the tential Progression chart, which has age along this side and time horizon along the vertical. So you get age and time horizon. But Elliot only introduced this chart in 1976 in his book. Before then he had a different chart. It looks the same, the two look very much alike, but they're not. And in terms of data, they look very much alike also. But in terms of what you have here is your earnings progression data sheet. And you have age along the bottom. Afraid this is faded somewhat. And along the side, you have wage the actual wage paid. As a result, you have a sort of jagged line for individuals as you go along, but they stay within each of the bands. Okay? Now, in five minutes, okay, in Japan, they sent a person over to do his PhD at the University of Wisconsin, and he put together, you'll notice age along this side and wage along this side. You find very similar data, but the identical structure of it in the process. Most US firms do not keep this information on their own employees. So one of his other assignments was to find out where in the United States information, and of course, the government kept it as part of a census bureau. And sure enough, here is the age wage of the US 1967 data. Since then, the Japanese have kept this data on the US. This is one from 1979, data printed almost 20 years later. One. The UK and Japan. And here's, similar data on the EC and Japan. Again, they take a slightly different grouping of people rather than by what band they're in, by whether they're white collar or blue collar as a result of this. Okay, the question and the biggest bang for the buck is that there are seven tools in terms of quality. The seven tools, one of which is a pareto. You rank your types of errors according to percentage. In this particular case, we're talking about circuit pack failures, and again, whether component failures, a wrong component, soldering, defect, et cetera. In other words, where is the defect coming in? So that's something you drew internally. We have not yet developed the seven tools, which not that I know of, that have been developed over the years, basically by the Japanese, but adopted by the Americans. The key to this, I think, in terms of what you bang for the buck as a consultant as well as for academics, is right there in role misplacement with the individual, where you have only two PhDs in the United States 30 years apart, came up with identical information. One by Ron Cappell, was on his website again, also in 1999 in Toronto. Same data, identical. Glenn meltred claims slightly different. He claims that the 50% is slightly higher. Okay, so what we got hit here is a Peretta, where you have 49% ever rate. You have 23% too high. The people belong in next category and next role above and 26% too low. Today, every manager is saving those people who are too high to compensate for those who are too low, who can't do the work. And so those are his stars. He's hanging on to them as hard as he can, and meanwhile, he's trying to get rid of the others. So that's enough for now. But two things. One, there is an opening, and number two, the Japanese are already doing it. General Motors has told us to take a walk, ford has told us to take a walk and guess who has already adopted this. In 1969. At the same time, or about six months before it was rejected at the American Psychological Association, the equity theories were rejected, an attack on Stacy Adams and also carried implications for anyone else in that camp, including Elliot Jacks at the same time. It was adopted that spring in 69 by the Vindicarette, which is equivalent to conference board in the US. And basically it gave from six carets to it gave three things. One, a study group from 65 to 69 which visited Glacier. Yes. They visited Glacier. I asked Elliot about it and he said he knew about it, but he didn't meet with them. So I need some help in the UK to do some more tracking. But Wilfred Bron had already joined the government, so he wasn't there. Either. They weren't interested in meeting Wilfred or Elliot. They were interested in how it worked at Glacier because they adopted. And in 69, after about six months or a year ringy discussion group, they adopted for the six caretzen. That was in April 69. And they also issued the manager once removed. This is called a Setai system, which is how you promote, how you hire and how you retire people and move them out to secondary companies. So it's how you handle people, not the Mengo system, which is based on length of time, which is against all of our economic theories and therefore got a lot of press. It's not true. So this was adopted by Toyota as well, but not by General. The companies in the US that have adopted this is General Electric, Avon, Shell, which we heard about sonoco, JPMorgan Chase and Microsoft. Those we know have adopted both.
Major organizations and consulting firms that provide Requisite Organization-based services
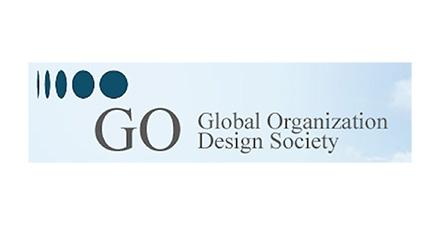